Testing
There were a total of four tests which were done, the force to turn the handle using a standard ratchet, time to raise/lower one foot using both the ratchet and a power drill, maximum expected load, and force to tip. The maximum expected load test was the trickiest and most crucial test to run. Unfortunately due to the critical features of the assembly being the ACME threads themselves, this test was done as a go/no-go test.
Results
The end product of the full load testing was a complete success. There were no failures when the load was applied. When the table was also shaken the ACME threaded rods were not damaged, neither was the nut that had been welded inside of the timing belt pulley. However, when unloading the table it was noticed that there was significantly more rocking in the table than when loading. Upon disassembly many of the bolts were found to be very loose providing almost no clamping force, this easily accounted for the increased rocking of the table and needs to be taken into consideration when assembling the table to apply more force to tightening the bolts so they do not become loose after being jostled.
In relation to the analysis completed the finished product was representative of the work that had been done. The critical load was able to be supported as predicted by the column analysis, the forces required to start the timing belt was within 5lbf of the estimated, and the time it took to raise the platform was directly related to the RPM able to be imparted onto the outside pulley, with one rotation raising the table exactly 0.167in as defined by the 6 TPI ACME rod.

The first idea for how to load 800lbs onto the chassis was to get sandbags and load them onto the chassis one at a time. This however would have resulted in needing a lot of sand without having further use for the large amount of weight that it constituted.
The next idea that was brought to mind was using a uniform water tank (left) to use water as the weight. This had many potential problems, the primary concern was that if the structure began to buckle with the tank on it, the water would shift and compound the load that was causing the failure. This would result in the chassis being incredibly damaged, as well as possibly having the container end up on the floor, damaging it and anything that was around. This problem had the potential to be fixed by using the crane in the FLUKE lab to act as a catch should failure start to occur, but at the time that the test needed to be completed the equipment to do so was no available.
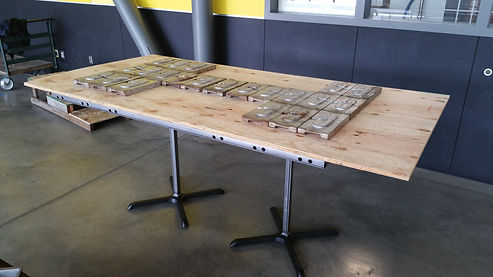
Due to the inability to run the testing with the water tank the only feasible option left was to manually load individual weights onto the table in as distributed a load as possible. A sheet of plywood was used as the platform to load the weights onto. On the right is the table loaded with all of the available known weights, these weights along with the sheet of plywood came to be 506lbf.
At this point I still needed weights, upon asking Dr. Johnson if he had weights available he pointed me to ingot casts in the foundry, which
there were a large number. Weighing each of them showed theywere 23lbs a piece. The video below shows the table fully loaded up to 853lbs, as well as the chassis being jostled and rocked back and forth to simulate any sudden shifts in the weight of the table.